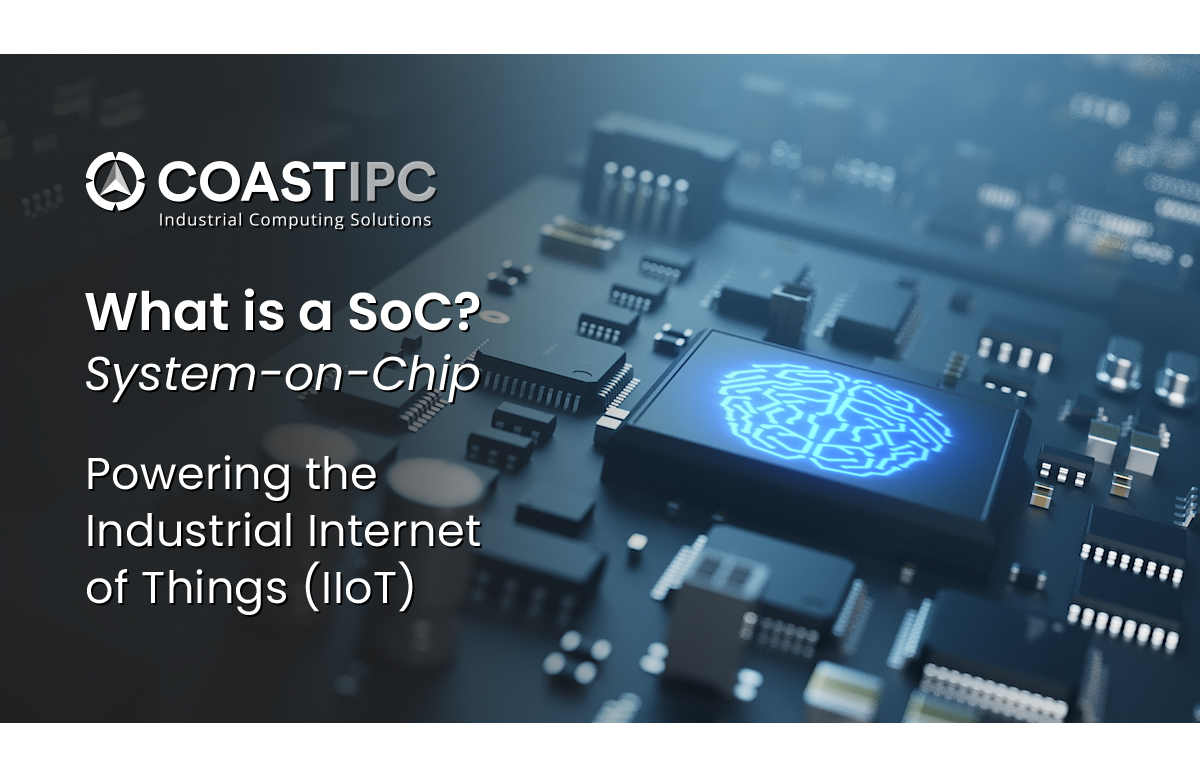
A system-on-chip (SoC), as its name implies, is an entire computer system or platform integrated onto a single device or integrated circuit. Within the circuit, an SoC includes a central processing unit (CPU), a graphical processing unit (GPU), memory, external interfaces for wireless communication (Bluetooth, Wi-Fi, etc.), and external interface controllers for wired communication (USB, HDMI, Ethernet, etc.) and other controllers (USART, SPI, I2C, etc.) to facilitate interconnectivity with peripheral devices and integration of the SoC into a larger system.
Advantages and Disadvantages of SoC Technology
With SoC technology rapidly evolving and proliferating into many different types of applications, some may wonder whether the time is right to incorporate the technology into their systems, products, and projects.
Offering considerable footprint, power consumption, and unit cost savings versus traditional multi-component systems, SoCs are a natural choice for mobile, robotic, embedded, and other small-form-factor applications. Their power efficiency makes them ideal for use in battery-powered systems and where heat dissipation may be a challenge. Many SoCs are no larger than 1 inch square. Compare this to even a small single-board computer (SBC), where you need space for individual components — CPU, memory, external interfaces, circuitry, and controllers — and the flexibility in deployment of an SoC solution becomes apparent.
SoCs that are intended for general use and are not application-specific in their design are typically manufactured in high volume, taking advantages of manufacturing economies of scale. This translates into high market availability, cost-effectiveness (costs generally come down as manufacturing volumes go up), and verifiability — integrated circuits typically undergo a lot of verification and testing prior to mass production.
Looking to the other side of the equation and remembering that not all technology is a great fit for every application, there are some disadvantages to SoCs. First, SoCs lack adaptability. The performance characteristics of the system are fixed and cannot be changed, upgraded, or enhanced. For example, if a system doesn’t offer enough memory for your application needs, you can’t simply add more. Similarly, if an element of the circuit fails, you need to replace the entire system, since everything is contained in a single chip.
If you require an application-specific or a customized SoC, development costs are very high. In fact, they might be prohibitive, particularly if your usage volumes are low, since this will prevent realization of economies of scale in manufacturing and may make it impossible to recover your investment. Traditional computer system architecture and design continue to hold the upper hand when it comes to absolute computing power. For intense processing applications, SoCs are still a long way from being able to rival the performance capability of a mainboard-based system that uses discrete components with dedicated purposes.
Use Cases
In the OEM and manufacturing sectors, SoCs are actively being used to drive the next generation of Industrial Internet of Things (IIoT) connectivity and communication devices with enhanced processing capability and reduced power consumption. With the number of devices and sensors continuing to grow in the IIoT space, so too are the resources and interfaces needed to manage them in harmony. Utilizing SoC technology in embedded processing systems enables deployment in power-constrained environments with both wired and wireless connectivity.
Edge computing can also benefit from SoC technology, as small industrial PCs (IPCs) are increasingly being used to perform specific, dedicated preprocessing, communication, and decision-making tasks related to machine vision and non-vision systems and sensors, intersystem connectivity, and cloud-based integration within the factory or industrial automation floor.
Robotics presents yet another avenue for SoC success. Mobile and battery-powered autonomous mobile robots (AMRs) and autonomous guided vehicles (AGVs) rely on lightweight and low-powered electronics to manage the various sensors they need to support navigation, decision making, and communication. SoC-based solutions are an ideal fit to facilitate those interconnectivity, data processing, and off-platform communication requirements.
SoCs vs. SoMs
Another concept becoming more prevalent in technology circles, particularly in industrial and embedded computing, is system-on-module (SoM). This is distinctly different from SoC in that an SoM is circuit card–based, and while it may include an SoC as part of its design, it also has space for other peripheral devices, such as memory or other interfaces, and is designed to plug into an expansion slot on an embedded or industrial PC mainboard or carrier card.
Navigating the different aspects of embedded technology, including system-on-chip offerings, can be challenging with the number of new products, technology advancements, and addressable applications being introduced. The CoastIPC team brings a wide range of knowledge and can help you navigate the different options available today. We can work with you to understand your unique application needs and can propose solutions that meet your requirements and budget.
For more information about system-on-chip, embedded, or industrial computing, the benefits and advantages of each, and how they might suit your application, please contact our product experts by emailing [email protected], submitting a form here, or calling 866-412-6278.